UK researchers develop greener, more sustainable ways to recover metals from electronic waste
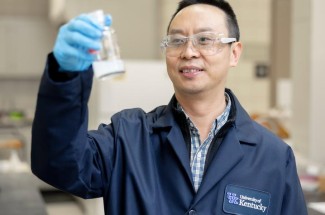
As electronic waste (e-waste) piles up globally, researchers at the University of Kentucky Martin-Gatton College of Agriculture, Food and Environment and the Stanley and Karen Pigman College of Engineering are spearheading innovative methods to recover valuable metals from discarded devices and industrial waste.
E-waste — including smartphones, laptops and spent batteries — contains critical materials such as lithium, cobalt and nickel essential for electrochemical energy storage applications. However, traditional recycling methods often rely on harsh chemicals and energy-intensive processes, creating environmental and economic challenges.
Now, researchers are developing innovative solutions to make obtaining these metals safer, more efficient and sustainable.
With a $1 million grant from the U.S. Department of Energy, a team led by Jian Shi, an associate professor in the Department of Biosystems and Agricultural Engineering, is advancing a greener way of extraction called hydrophobic deep eutectic solvents (DESs). These plant-based solvents offer a novel alternative to traditional recovery methods that rely on high-temperature processes and/or petroleum-based solvents.
“This isn’t just about improving recovery rates,” said Shi, the grant’s principal investigator. “It’s about building a system that values people, the planet and the future of our industries.”
The research team includes Isabel C. Escobar, co-investigator on the grant; Rick Honaker, professor of mining engineering; and Qing Shao, an assistant professor of chemical engineering in the Pigman College of Engineering. They’ve zeroed in on four critical areas where DESs can make a transformative impact.
Selective metal recovery
Recovering metals from e-waste is like mining in miniature. But unlike ores extracted from the earth, e-waste contains valuable and unwanted materials.
“We’ve worked on reclaiming minerals and metals from waste materials for decades — bringing together expertise from across UK’s campus to tackle this project,” Honaker said. “Sustainability is a key piece of this work, and we look forward to the advances these plant-based solvents will offer.”
Traditional methods lack precision, often extracting multiple metals simultaneously, which leads to contamination and requires additional steps to achieve the desired purity.
By tailoring the chemical properties of each solvent to target specific metals, the research team can selectively recover high-purity lithium, cobalt or nickel from complex waste streams. This precision reduces contamination, simplifies downstream processing and improves the overall efficiency of recovery operations.
The team is leveraging newer tools like molecular simulations and machine learning. By analyzing the composition of e-waste and designing DESs tailored to specific feedstocks, they can optimize recovery rates while minimizing waste.
“By focusing on the selectivity over individual metals, we’re improving efficiency and reducing waste and contamination in the final product,” Shao said.
This selective recovery is vital for industries like electric vehicle battery manufacturing, where even minor impurities can compromise performance.
Cleaner chemistry and safer workplaces
Traditional recovery methods rely heavily on sulfuric acid and other highly corrosive chemicals. These substances pose significant risks to workers and generate hazardous waste that can harm the environment. Equipment corrosion from these chemicals also drives up costs and downtime.
DESs provide a greener alternative. Derived from renewable materials like plant phenolics and organic acids, these solvents are biodegradable, less toxic and operate under mild conditions. This reduces worker risks, minimizes the need for costly safety measures and lowers the environmental impact of the recovery process.
The shift to safer, greener chemistry represents a step forward for industries seeking to balance efficiency with environmental responsibility.
Minimizing waste through solvent recycling
Waste generation is one of the most significant drawbacks of current recovery systems. Conventional solvents are often used once and discarded, contributing to high operational costs and environmental harm.
Escobar’s team is developing novel membrane separation technologies that will allow these plant-based solvents to be reused repeatedly without losing their ability to recover critical metals. This innovation reduces the volume of waste generated and lowers the cost for industries adopting the technology.
“This is about creating a system where materials are continuously reused,” said Escobar, a professor of chemical engineering and Chellgren Endowed Chair. “It’s a smarter way to manage resources.”
By integrating solvent recycling into the recovery process, the team is laying the groundwork for a circular economy in critical metal recovery.
Partnership for better science
This project offers an opportunity for the UK researchers to collaborate with scientists at the facilities of the Department of Energy’s Oak Ridge National Laboratory (ORNL). This provides training opportunities for undergraduate and graduate students as well as postdoc researchers. ORNL offers much-needed infrastructure and expertise including the Spallation Neutron Source, Center for Nanophase Materials Sciences and Nuclear Magnetic Resonance facilities.
“This project goes beyond metal recovery. It’s about creating safer solutions for workers and training for the next generation of scientists and engineers,” Shi said. “We hope to develop an approach which is better for the planet and more cost-effective for industries. By implementing greener and more efficient technologies, we’re making strides toward a sustainable future.”
BAE is a partnership between Martin-Gatton CAFE and the Stanley and Karen Pigman College of Engineering. To learn more, visit https://www.engr.uky.edu/research-faculty/departments/biosystems-agricultural-engineering.
This material is based upon work supported by the Department of Energy under Award Number DE-SC0025346. This report was prepared as an account of work sponsored by an agency of the United States Government. Neither the United States Government nor any agency thereof, nor any of their employees, makes any warranty, express or implied, or assumes any legal liability or responsibility for the accuracy, completeness, or usefulness of any information, apparatus, product, or process disclosed, or represents that its use would not infringe privately owned rights. Reference herein to any specific commercial product, process, or service by trade name, trademark, manufacturer, or otherwise does not necessarily constitute or imply its endorsement, recommendation, or favoring by the United States Government or any agency thereof. The views and opinions of authors expressed herein do not necessarily state or reflect those of the United States Government or any agency thereof.
The Oak Ridge National Laboratory is supported by the Office of Science of the U.S. Department of Energy. The Office of Science is the single largest supporter of basic research in the physical sciences in the United States and is working to address some of the most pressing challenges of our time. For more information, please visit science.energy.gov.