Coal to critical elements: $5 million DOE award propels UK’s refined materials work
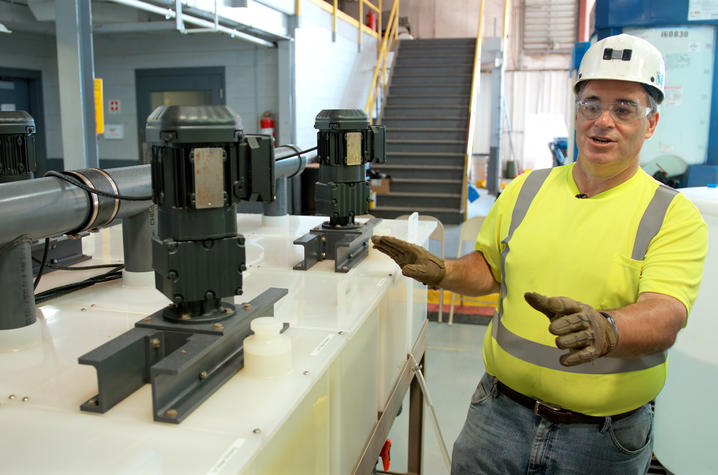
A team of engineers at the University of Kentucky, in collaboration with researchers at other universities, will work on a system to transform coal into high-value materials.
The project titled “Bipartisan Infrastructure Law - BIL - Development of a Strategic Materials Production System for Rare Earth Metals, Graphite and Other Critical Materials,” is supported by a $5 million award from the U.S. Department of Energy (DOE).
“The ability to extract critical minerals and elements from coal is a game-changer. It allows us to tap into a domestic resource, turning what was once overlooked into a valuable supply of materials essential for clean energy, technology and national security. This innovation is a sustainable and resilient path forward,” said Rick Honaker, Ph.D., professor of mining engineering in the UK Stanley and Karen Pigman College of Engineering, a University Research Professor and principal investigator of the award.
Honaker has assembled a team of experienced researchers as co-investigators on the project, including Jack Groppo, Ph.D., a professor in the Department of Mining Engineering and researcher at the UK Center for Applied Energy Research (CAER); Bin Ji, Ph.D., an assistant research professor in the Department of Mining Engineering; and Matthew Weisenberger, Ph.D., an adjunct assistant professor of chemical and materials engineering and CAER associate director of the Carbon Materials Research Group.
The project will focus on critical minerals and rare earth elements — materials that are essential to modern technologies, clean energy and economic security but vulnerable to supply chain disruptions.
The engineering team will work to extract those valuable materials and graphite from a specific type of coal that naturally contains high concentrations of these materials. They will extract and purify rare earth elements like dysprosium, neodymium, yttrium, praseodymium and gadolinium, and then convert them into metal products. These elements are used in magnets, batteries and electronic devices.
“For decades, our work at CAER has focused on reclaiming minerals and metals from waste materials. These are vital for clean energy, electronics and defense, and our process demonstrates how industrial waste can become a critical resource for the future,” said Groppo, who has helped establish UK as a global leader in electronics recycling.
Critical minerals like cobalt, nickel, manganese and lithium will be produced at a minimum of 90% purity. These metals aid the overall capacity and stability of the battery cathode — where the energy is stored.
The engineers will also upgrade the coal’s carbon material by removing impurities and refining it to create ultra-pure graphite (99.95% purity). Graphite is a key component in lithium-ion batteries, which are found in products ranging from cell phones to electric vehicle batteries.
“Our Carbon Materials Research Group is focused on turning waste coal into valuable, usable materials,” said Weisenberger. “This project brings together our research expertise at a crucial time to help ensure our Commonwealth and country have the needed materials for the future.”
Another part of the project focuses on installing and testing new processes in a pilot plant to reduce production costs of rare earth oxides and critical minerals by 20%. Rare earth oxides are typically powders that exhibit unique magnetic and electronic properties — crucial for clean energy technologies, electronics and modern industrial processes.
The team will also work to remove unwanted metals like iron and aluminum with ion exchange columns.
“We will use an innovative process called microbubble-assisted solvent extraction to separate and concentrate the valuable elements,” said Honaker. “We will then develop optimum extractant chemistry and a process train to produce highly purified individual rare earth elements. Once purified, the individual rare earth oxides will be converted to metal by ionic liquid low-temperature processing and plasma distillation at bench-scale.”
The research team, which includes researchers at the University of Alabama and Virginia Tech, will take the data collected from the pilot plant to better understand how to scale up these processes to a commercial plant capable of producing 1-3 tonnes of purified rare earth oxides per day.
This project highlights CAER and Pigman College of Engineering’s research expertise in two of the university’s research priority areas: Energy and Materials Science. Both seek to find innovative solutions to address industry challenges and position the Commonwealth to become a global leader in a competitive materials market.
This material is based upon work supported by the Department of Energy under Award Number DE-FE0032505. This report was prepared as an account of work sponsored by an agency of the United States Government. Neither the United States Government nor any agency thereof, nor any of their employees, makes any warranty, express or implied, or assumes any legal liability or responsibility for the accuracy, completeness, or usefulness of any information, apparatus, product, or process disclosed, or represents that its use would not infringe privately owned rights. Reference herein to any specific commercial product, process, or service by trade name, trademark, manufacturer, or otherwise does not necessarily constitute or imply its endorsement, recommendation, or favoring by the United States Government or any agency thereof. The views and opinions of authors expressed herein do not necessarily state or reflect those of the United States Government or any agency thereof.
More from this series Research Priorities - Energy
Credits
Words: Lindsay Travis (Research Communications)
Photos: CAER and Pigman College of Engineering and Jeremy Blackburn (Research Communications)