UK researchers are leaders in recovering materials that power our world
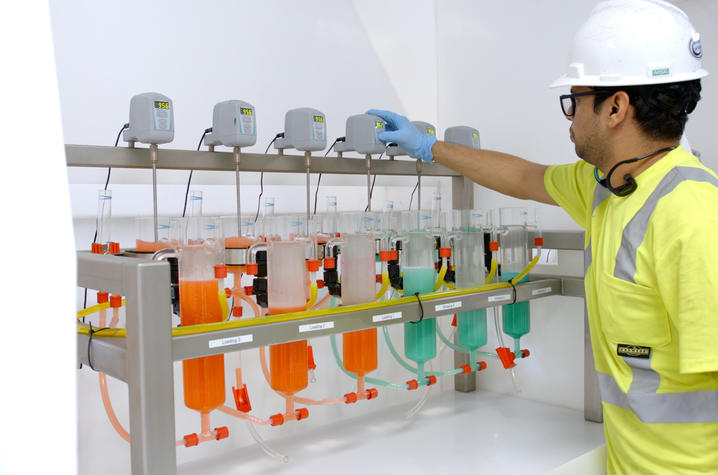
No matter who you talk to in the manufacturing, energy and industrial fields the same themes arise. Renewable energy and new, “green” materials are important to their missions and, ultimately, their customers.
Whether it is purchasing more renewable energy, electrifying their vehicle fleet, investing in batteries and energy storage, or removing carbon dioxide from materials and processes, the era of sustainability is here.
There is one linchpin that will be the key to developing sustainable technology in these areas: critical minerals.
“If you want to build electric vehicles, make batteries, build wind turbines, develop solar and manufacture any electronic device, you need these minerals,” said Rick Honaker, professor in the Department of Mining Engineering at the University of Kentucky’s College of Engineering. “You need things like cobalt, lithium, neodymium, praseodymium and dysprosium.”
The major problem for our current and future generations? There are only two ways to obtain critical minerals. We can mine for those materials. Or we can develop more sustainable technologies and extract those materials from our current world via electronics recycling and byproduct utilization and recovery.
The good news for Kentucky is due to a major investment from the UK Office of the Vice President for Research, the UK Center for Applied Energy Research (CAER) and the UK College of Engineering, UK is acting now to ensure the Commonwealth will be a national and international leader in the development of a booming critical minerals industry.
A significant domestic and international problem
According to an International Energy Agency (IEA) report titled, “The Role of Critical Minerals in Clean Energy Transitions,” the transition to clean energy presents a unique global challenge. “A typical electric car requires six times the mineral inputs of a conventional car, and an onshore wind plant requires nine times more mineral resources than a similarly sized gas-fired power plant,” the report states.
“Today, the data shows a looming mismatch between the world’s strengthened climate ambitions and the availability of critical minerals that are essential to realizing those ambitions,” said Fatih Birol, executive director of the IEA. “The challenges are not insurmountable, but governments must give clear signals about how they plan to turn their climate pledges into action. By acting now and acting together, they can significantly reduce the risks of price volatility and supply disruptions.”
The critical minerals supply chain issues facing the United States have been well-known by those studying, investigating and working in impacted industries for years. However, more recent conversations and calls to action have brought the issue to the forefront to new audiences.
In February 2022, the U.S. Geological Survey (USGS) released its “2022 Final List of Critical Minerals,” identifying 50 minerals that are essential to national security and prosperity.
The minerals listed by the USGS are the building blocks of our modern society. It contains traditional materials familiar to all of us like aluminum, nickel and zinc. Also listed are materials that are essential to energy production and storage and all home and business electronics that dominate our lives. Those include materials like lithium, graphite and manganese.
These 50 minerals are included on this list for various reasons. Generally, they are not available in large enough supplies here in the U.S. Not only are many of these minerals not available domestically, but most are also only available in countries without stable governments, are currently at war, or are not necessarily friendly to U.S. or western interests.
Jim Farley, chief executive officer of Ford Motor Company, spoke about these issues at an event in Detroit in September 2021. He said, "We have to bring battery production here, but the supply chain has to go all the way to the mines. That's where the real cost is and people in the U.S. don't want mining in their neighborhoods. So, are we going to import lithium and pull cobalt from nation-states that have child labor and all sorts of corruption or are we going to get serious about mining? We have to solve these things and we don't have much time."
UK’s response: Building one of the nation’s foremost critical minerals R&D operations
The University of Kentucky has been developing research expertise and know-how in the critical minerals space for many years.
Honaker has operated a rare earth element pilot plant in Providence, Kentucky, for the past four years. That plant, located in the Western Kentucky coalfields, has developed engineering processes to capture a variety of metals and minerals directly from coal middlings, a byproduct of coal washing and preparation. The pilot plant operated continuously at a rate of 100 pounds per hour of solids and produced 10 to 100 grams per day of 90% rare earth oxide mix.
Honaker, Jack Groppo, a researcher at CAER and mining engineering professor, and Josh Werner, assistant professor in mining engineering, have worked in Eastern Kentucky coalfields, too. A large source of domestic rare earth elements and other minerals can be found in Eastern Kentucky.
Working with coarse refuse in Fire Clay, a prominent coal seam in Eastern Kentucky, the research team demonstrated scaled production of high-purity rare earth oxide mix from coal refuse sources using innovative technologies that will reduce cost and improve environmental outcomes. Their project estimates there are 29,000 metric tons of rare earth elements and 55,000 tons of other critical metals in the Fire Clay coarse refuse. Those metals have a $6.9 billion total value.
In addition, Groppo and Werner have established UK as a global leader in electronics recycling. As our lives have become more digital, all the devices that we use each and every day – from computers to mobile phones to video gaming systems – only have a certain lifespan. Most of the materials from those devices are tossed into a landfill. UK has launched a closed-loop recycling program that seeks to capture the valuable metals contained in those devices and re-introduce them into the marketplace.
“Having expertise in one of these areas is significant,” said Rodney Andrews, director of CAER and senior associate vice president for research at UK. “The fact that we have experts in all of these areas and successfully demonstrated these technologies is a big deal. It provides the university a unique advantage and showcases to prospective collaborators that UK is the place for this research.”
A ‘SMaRT’ Kentucky investment
The good news for Kentucky is that UK is bringing all this unique expertise under one roof. CAER will be home to one of the foremost critical minerals research and development operations in the country: The University of Kentucky Strategic Materials and Recovery Technologies (SMaRT) Center.
Honaker is moving his pilot plant to CAER to continue further research. With a strategic investment from the UK Office of the Vice President for Research (OVPR), CAER was also able to acquire a metallurgical research laboratory and equipment to accelerate the University’s research efforts.
According to UK Vice President for Research Lisa Cassis, this investment is a great example of the university’s Research Priority Areas program. As part of UK’s strategic plan, the OVPR selected seven research areas on which to focus, including energy.
“One of the rationales for developing the Research Priority Areas was to attack Kentucky problems,” said Cassis. “We know that when we find solutions to Kentucky issues, they have a global impact. Clearly, one of the most pressing problems in energy today is critical minerals. We are thrilled to invest in this SMaRT Center and look forward to seeing what this talented group of researchers does next.”
Developing a talent pipeline
Equally important to this research initiative is the development of highly-training technicians, scientists and engineers.
“We are at the forefront of what I believe will be a new industry in the United States,” said Groppo. “Training the generation that will lead this industry has been a major focus of our work. Frankly, we hope this industry takes off, and we hope it takes off right here in the Commonwealth of Kentucky.”
These burgeoning programs have changed the way UK trains mining engineers. Mining engineering students still learn about materials separations as they have for generations. But instead of utilizing traditionally mined materials, they are utilizing end-of-life electronics, too. As the field grows, these UK students will be uniquely prepared to drive innovation and inspire creativity in the marketplace.
“These are the skills our students will need in tomorrow’s job market," said Groppo. “There is such demand for critical minerals that we will need a multifaceted approach to meet industrial demand. We will still need to mine for minerals. But we will need to capture metals from end-of-life materials, too. Being able to teach UK students both of these skill sets will be increasingly important.”
More from this series Research Priorities - Energy
Credits
David Melanson (Center for Applied Energy Research)